Digitization efforts have vastly improved manufacturing efficiency over the last decades. The current drivers of progress are AI and machine-learning-enabled networks that connect data, processes, people, services, and systems – such as barcode systems for manufacturing.
To ensure well-coordinated, cost-efficient production processes, manufacturers have to optimize every part of their value chain. In particular, they must ensure friction-free communication between departments, with suppliers, and with customers.
Barcode systems are fundamental to speedy, reliable communication in the industrial sector. Barcoding is one of the most efficient and accurate ways of connecting physical objects to digital data.
In this article, we’ll examine the part these codes play in digitizing manufacturing workflows.
Why is it so important for manufacturers to implement barcode systems?
Real-time data exchange is a cornerstone of optimized manufacturing processes, as it turns products and equipment into parts of an overarching system. Reliable information on them needs to be available at any point in the production and distribution processes, because every error translates into losses in quality, productivity, and revenue.
Yet the full potential of industrial digitization is still rarely leveraged across the entire complex ecosystem of a modern factory. Countless manufacturers still heavily rely on manual data entry. This exposes manufacturing processes to human error, resulting in friction between the links of the affected value chains.
The consequences are lost productivity and expenditures – much of it avoidable. Gartner reports that poor data quality, in particular, costs the average organization almost $13 million annually. Consequently, manufacturing businesses should avoid relying on such error-prone processes at all costs.
Companies need to rationalize each step within their production to exploit their factories’ full potential and maximize revenue. By implementing barcode systems for this purpose, you enable staff to precisely track item quantities and locations at any point of the production chain. A quick scan is enough to log or access the relevant information.
Creating such a system takes only a few simple steps.
Step by step: How to implement a barcode system in manufacturing
Let’s now take a look at the key steps involved in designing and rolling out a barcode system in manufacturing.
Step 1: Create barcode labels
For your barcoding system, you will need barcodes to label or mark the materials and finished goods with. For this, you first have to determine what data you’d like to store and pick a barcode standard that suits your requirements.
There are two broad categories of barcodes: one-dimensional (1D) and two-dimensional (2D).
1D barcodes, or linear barcodes, encode data horizontally in parallel vertical bars and spaces of varying widths. They are generally easier and faster to scan, and are suitable for simple identification tasks. Common 1D codes for manufacturing include:
- Code 128: packaging, shipping, and tracking
- GS1-128: logistics, supply chain, standardized exchange
- Code 39: product labeling
- UPC/EAN: product identification, retail packaging
2D barcodes, such as QR codes, encode data horizontally and vertically. They can thus store more data than 1D barcodes in the same space, and are typically smaller. Popular 2D barcodes for manufacturing include:
- Data Matrix: small parts, electronics
- QR code: inventory, product info, digital links
- PDF417: shipping labels, inventory management
For internal use, barcodes can be generated using free online generator tools. However, if you want them to be globally compatible, consider implementing official standards, such as GS1 barcodes.
Step 2: Align the system with your software ecosystem
Once goods are labeled, employees can easily scan the attached barcodes for a variety of purposes. For this, you can equip them with conventional hardware scanners – but increasingly, businesses leverage budget mobile devices such as smartphones or tablets.
Whether you opt for conventional hardware or for smartphones running a Barcode Scanner SDK, the solution must be integrated seamlessly into your existing software ecosystem. This guarantees the frictionless data transfer between the scanning devices and the backend software, such as your ERP or CMMS.
Step 3: Establish the entire barcoding process
Before rolling out your new system, you should test all the processes involved. This includes the labeling, the scanning process itself, and updating information in the backend software system. For example, carefully consider where to place the barcode label on each item to ensure it is not obscured.
Step 4: Roll out the new system step-by-step
Most manufacturers ultimately want to optimize their whole production process using a barcode system – from receiving raw materials to packing the final goods. Tackling all these areas at once is quite challenging, however. If not executed properly, such a project will increase friction rather than reduce it.
It is best to start small, for instance, by implementing the system for either raw materials or finished goods first. This way, initial difficulties and the resulting adjustments to the system won’t affect the whole production chain, but just a segment of it.
💡 Note:
To barcode raw materials, it is helpful to align the used symbologies with your suppliers. As barcoding in manufacturing has become common practice, this is now just another standard procedure for most suppliers.
By properly planning and implementing a barcode system, manufacturers can significantly reduce friction losses in production processes. Reducing manual data entry and thus automating critical steps in the manufacturing process has a considerable ROI and future-proofs workflows.
Apart from streamlining production itself, barcode systems can add value in a number of other ways. Let’s explore some of them.
Potential applications for your new barcode scanner system
Keeping an eye on every step in manufacturing operations can quickly become overwhelming – especially as they generate more and more data.
Solutions like enterprise resource planning (ERP) and warehouse management systems (WMS) are supposed to solve this challenge, gathering and connecting all data. Relying on manual data entry severely limits their potential, however. By adding a barcode system to the mix, manufacturers can properly optimize their operations.
There are, in fact, many common operations that can benefit from barcode scanning:
- Inventory management
- Order picking
- Shipping and receiving
- Batch tracking
- Asset tracking
- Quality control
Let’s take a look at each of these applications and see how barcode scanning can enhance them.
Inventory management
To enhance inventory management, businesses can label all inventory items with barcodes. They can then be scanned during receiving, picking, and shipping, enabling real-time inventory level updates. Accurate stock level information, in turn, enables faster operations.
For instance, when construction parts are delivered, workers could immediately get a notification and proceed with the relevant workflows.
Order picking
Pick-by-scan systems significantly speed up order picking. Here, warehouse workers are guided through warehouses with barcode scanning.
For this, smart devices equipped with a barcode scanner functionality receive a picking list from a WMS or ERP system. The list includes the items and their locations. Warehouse workers are then guided to the item, where they confirm the pick with a scan. Now, the system can automatically check off the picking lists and generate the shipping documents.
Shipping and receiving
During shipping and receiving, barcode scans can confirm that the correct items are being sent to the right destination and check incoming shipments against purchase orders. Inventory levels are also updated immediately.
Batch tracking
Effective batch tracking is essential for recall management, as it enables the pinpointing and retrieval of affected batches in case of a product recall. When each batch is marked with a specific barcode, these can be scanned at every production step, allowing batches to be traced back efficiently.
Quality control
Barcoding raw materials, components, and finished goods improves visibility into every step of production. At each quality control checkpoint, barcodes can be scanned to log inspection results – or to access them. This ensures that only items meeting requirements proceed to the next step.
Asset tracking
The unique barcode tag assigned to an asset can be scanned to provide immediate updates on its location, status, and condition to a backend system.
Implementation challenges
Whatever the exact application, manufacturing workflows present unique challenges for barcode system implementation. They include:
- Special environmental conditions: Harsh conditions like heat, dust, vibration, and chemicals can destroy ordinary barcode labels and impact sensitive barcode scanner technology.
- Barcode readability: Changing lighting conditions and poorly printed, smudged, damaged, or faded barcodes often test the limits of traditional barcode scanners.
- Data accuracy and consistency: Unreliable scans cause inventory discrepancies and traceability breakdowns.
- Ease of adoption: Employees have to be trained on the new workflows. If scanning is not intuitive, this is time-consuming and can lead to scanning errors.
- Maintenance and upkeep: Barcode scanners require maintenance to prevent downtime and data loss.
On the hardware side, the solution to these challenges is to use smartphones as barcode scanners. Ruggedized devices are explicitly designed to withstand harsh conditions. Once equipped with barcode scanner software, they reliably scan both 1D and 2D barcodes, even when these are damaged or blurry, and even in bad lighting conditions.
There are also usability and maintenance benefits: Since most employees are used to handling smart devices, training time and scanning errors are kept to a minimum. Commercial scanning solutions are regularly updated, preventing bugs and offering enhanced features.
As for the barcodes themselves, make sure to use appropriate inks and label materials, and explore direct part marking (DPM). 2D barcodes are often the better choice because they provide built-in error correction.
How your manufacturing business can benefit from using smartphones as barcode scanners
Smartphones offer numerous advantages for barcode scanning in factories, from cost to data quality and availability. Here are five of the most relevant.
Direct availability of information
Employees can access all relevant information on a particular item directly on the device – no additional hardware necessary. Tracking items, looking up stock levels, or finding the right equipment becomes a breeze thanks to AR overlays that display information on the screen.
Total Cost of Ownership (TCO)
Budget smartphones with a long battery life and suitable camera resolution are available for just around $300. Dedicated scanning devices with comparable accuracy and speed typically cost twice as much. Additionally, those devices need far more maintenance than smartphones or tablets.
Ease-of-use
Today, almost everyone owns a smartphone. Thus, employees do not need to learn to handle those devices before using them. Compared to dedicated scanners, easy-to-use mobile scanning tools on smart devices have a far shorter onboarding time.
Versatility
While inexpensive, standard laser scanners can only read 1D barcodes. However, versatile 2D symbologies such as QR Code are increasingly widespread – and they require camera-based scanners. For a time, this meant costly, dedicated imager scanners. Modern smartphones are the cheapest way to handle both types of codes.
Mobile smartphones are also highly flexible, with features such as batch scanning or find & pick serving to streamline common manufacturing and warehousing tasks.
Increased accuracy
Modern smartphones are equipped with high-resolution cameras. Combined with barcode scanner software, they decode barcodes quickly and accurately. Thanks to sophisticated image processing techniques based on machine-learning algorithms, they minimize misreads and other errors.
The Scanbot Barcode Scanner SDK: a mobile solution for manufacturers
The Scanbot Barcode Scanner SDK is a modern solution for mobile barcode scanning, whether for web or mobile apps.
Made for real-world conditions, it scans barcodes reliably even in challenging conditions. Features such as Batch Scanning, Multi Scanning, Find & Pick, and Scan & Count make it a versatile choice for a variety of common manufacturing workflows.
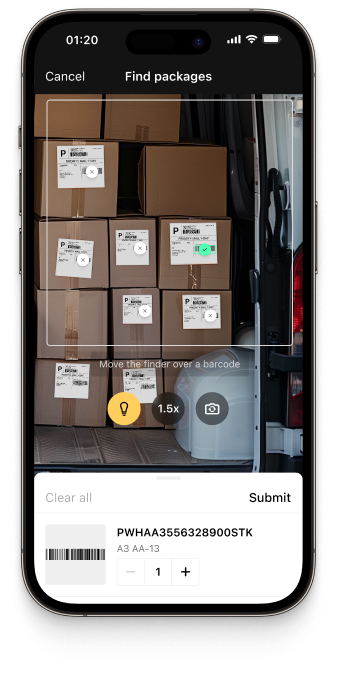
The included Ready-to-Use UI components cover multiple barcode scanning scenarios and allow you to integrate functionality into your app within an hour. Nonetheless, they offer a wide range of customization options.
Do you want to experience for yourself how the Scanbot Barcode Scanner SDK performs? Try our free barcode scanner demo apps.
Or read more about how Wolf System set up a highly efficient barcode system for its warehouse operations, thanks to the Scanbot Barcode Scanner SDK.
If you have any questions, message us at sdk@scanbot.io.