While traditional barcode labels are an effective way to track products, they often wear down, becoming unreadable over time. Robust product traceability, however, is critical for compliance.
What if a product needs to be identified or traced throughout its entire life span? What if the conditions will be harsh? Think of medical and military equipment, or airplane components.
The solution is to engrave the barcode directly into the material. In this blog post, we’ll explore Direct Part Marking (DPM) technology, its applications, and how to maximize readability.
What is direct part marking (DPM)?
The idea of direct part marking is to permanently apply a code onto the surface of an item. This makes DPM barcodes far more robust than labels, ensuring that parts and products can be identified and traced throughout their entire lifecycle.
There are several common DPM technologies manufacturers can use to this end. The DPM barcodes themselves are typically QR codes or Data Matrix codes, owing to their small footprint.
QR codes vs. Data Matrix codes for DPM
In industrial part marking, Data Matrix codes are generally preferred over QR codes. For one, they can store more data in the same space, making them ideal for marking small components. For another, their encoding makes them less prone to be misread, especially in challenging conditions such as poor lighting.
However, QR codes also have their advantages: Consumers readily recognize them and associate them with quick access to online information. Moreover, they can easily scan QR codes, using nothing but the default camera app on most modern smartphones. QR codes are therefore commonly used for web links, especially when the goal is consumer interaction.
Choosing the right marking method
Depending on the material and other factors, some direct part marking methods work better than others.
The three most common DPM methods are laser marking, dot peen marking, and chemical etching. Here is how they work – and when to use which:
- Laser marking uses a focused beam of light to create permanent marks on various materials. It can be used with most metals, plastics, glass, and ceramics. Laser marking is the most precise and fastest marking method. Furthermore, it is also the preferred choice for clean room applications, because the contamination risk is minimal.
- Dot peen marking uses an electromechanical engraving machine, usually a stylus or a pen, to rapidly engrave small dots. Dot peen marking is ideal for engraving on curved surfaces, soft metals, or when deep marking is required. Because the marked data can be changed easily and rapidly, it is also the preferred method for handling a lot of variety within products.
- Chemical etching selectively removes material from a surface to create specific patterns or shapes. This technique is specifically used on stainless steel and to produce high contrast.
Generally, laser marking is the go-to method for many DPM applications, especially in cases where precision, code durability and cleanliness are key. However, it does have some limitations such as a higher initial equipment cost.
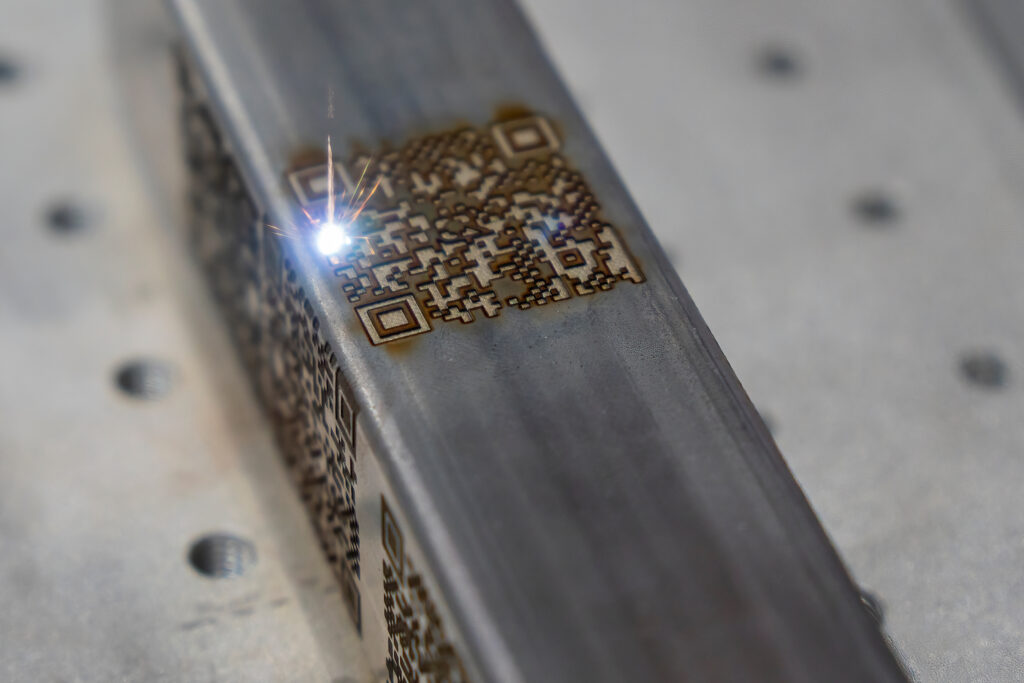
DPM technology: Benefits and challenges
DPM barcodes are highly durable and have a long life span. They can endure high temperatures, moisture, and corrosive environments, making them ideal for manufacturing in the military, medical, and aerospace industry. Barcodes engraved directly onto the object also minimize the risk of tampering, as they cannot be easily removed, altered or replaced – unlike traditional adhesive labels.
For these reasons, DPM technology ensures reliable identification of components and traceability throughout a product’s entire lifecycle.
However, the implementation and ongoing use of DPM barcodes does present challenges. To begin with, buying the marking equipment and training personnel to create and manage DPM codes can be capital-intensive. At the scanning end, the variety in component materials, including texture and color, can influence the accuracy of the DPM scanning results.
Lastly, there are industry standards and regulations to comply with. Different sectors have specific standards for barcode encoding. For example, the U.S. Department of Defense typically requires Item Unique Identification (IUID) as part of the compliance process for military applications. This ensures that all components in military vehicles such as tanks and fighter jets can be identified and traced easily throughout their lifecycle.
Industry applications
Direct part marking is used across various industries where identification and long-term traceability of components are essential. The technique became established in the automotive and aerospace industries first, but is now also found in healthcare, construction, electronics manufacturing, the food and beverage industry, and the energy sector.
NASA, for instance, has been using Data Matrix identification on their aerospace parts, and thereby exemplifies effective use of direct part marking in high-stakes environments. Some of our Scanbot SDK clients, such as SKF and Breww, have also implemented DPM to identify and trace parts across their supply chain – or their customers’.
Accurately scanning DPM barcodes
Direct part marking’s durability and reliability in harsh environments make it invaluable for product identification and traceability in sectors like aerospace, automotive, and healthcare.
However, certain factors should be considered when implementing DPM. The crucial concern is barcode readability, which can be affected by the materials’ textures and colors. Additionally, even DPM barcodes can become dirty or damaged. As a result, it’s advisable to invest in a scanning solution that can effectively address these challenges.
Our Scanbot Barcode Scanner SDK delivers reliable and fast scanning of both QR and Data Matrix codes, regardless of the surface material. Its powerful barcode scanning capabilities can be integrated into any mobile app or website, enabling fast and reliable scanning for all common 1D and 2D barcode symbologies, even under challenging conditions such as low light or damaged barcodes.
The SDK is available for all common platforms, including iOS, Android, Web, Windows, Linux, and cross-platform frameworks like Flutter, React Native, and .NET MAUI. One of its standout features is its ability to operate entirely offline, ensuring compliance with data protection regulations like GDPR and CCPA/CPRA.
In addition to basic scanning functionality, the SDK includes advanced features such as AR overlays for intuitive scanning, batch and multi-scanning capabilities, and customizable UI components. It is used by enterprises in a wide range of industries, including retail, logistics, healthcare, aviation, and manufacturing.
Interested to learn more? Try the Scanbot Barcode Scanner SDK yourself with the free demo app.