Wolf System digitized warehouse operations – eliminating delays and optimizing workflows
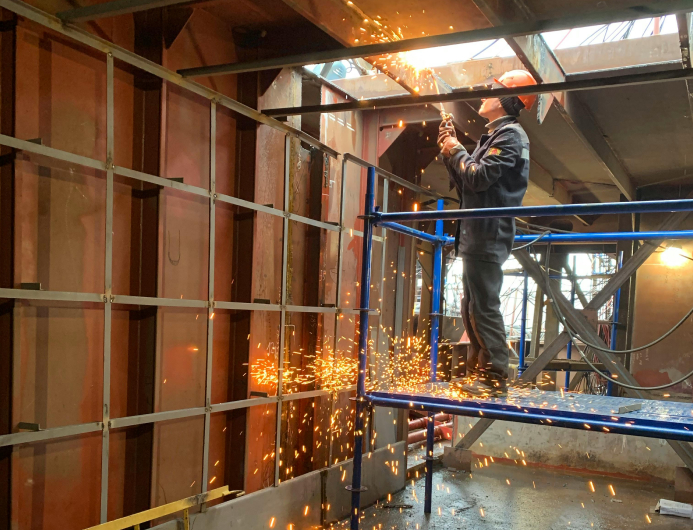
Goal
Wolf System GmbH sought to build a mobile web application with barcode scanning and document scanning functionality to digitize its inventory management system and improve parts traceability.
Challenge
This new warehouse management app needed a data capture solution that offered it all: fast, reliable barcode scanning and high-quality document scanning.
Solution
With Scanbot SDK, Wolf System GmbH got the whole package: fast and reliable barcode scanning and accurate document scanning in a progressive web application. A dedicated customer success manager and developer support made integration simple. Thanks to Scanbot SDK, Wolf System GmbH was able to streamline its warehouse management and ensure inventory accuracy.
Key Results
Digitized workflows
thanks to reliable barcode scanning and accurate document scanning
Accurate inventory data
thanks to real-time updates
Seamless operations
thanks to the elimination of slow and error-prone manual processes
Wolf System GmbH specializes in ready-made construction solutions. Every order is prefabricated in its production facilities. However, Wolf System GmbH faced multiple challenges in its warehouse management processes.
Incoming delivery notes were processed manually, delaying inventory updates and introducing errors. Storage locations, too, were poorly recorded. This caused a whole string of problems: Employees had to inquire about inventory via phone, which proved unreliable. Consequently, workers often couldn’t use the materials and products available in the warehouse for the task at hand. Significant amounts of time were lost, slowing down construction projects.
To improve warehouse management and – additionally – construction parts traceability, Wolf System GmbH developed an internal ERP system application. This web app would enable employees to directly add incoming goods to the inventory system, record their locations, and scan and automatically process delivery notes.
First, it introduced a barcode system: Warehouse locations and incoming construction material are now labeled with barcodes. Whenever materials are stored in the warehouse, workers scan their barcodes and the barcodes at the location, which updates the inventory system in real time. At the same time, the barcode system enhances construction part traceability after a project is completed.
To speed up delivery note processing, the Wolf System team initially tried sending smartphone pictures to the office. However, the image quality proved insufficient for back-end processing.
That’s why Wolf System GmbH searched for both barcode and document scanner software to integrate into the app.
“The open-source solutions we tried were slow and inaccurate. With Scanbot SDK, we got the whole package. The integration was fast and easy, and we are highly satisfied with their solutions. The SDKs are saving us a good amount of time.”
Scanbot SDK convinces with superior performance and reliable support
The Wolf System team evaluated several barcode scanner SDKs and found that the Scanbot SDK provided the most reliable performance. Open-source solutions were too slow, and Scanbot SDK’s competent and fast support added to the score. Thanks to this positive experience, the team decided on the Scanbot Document Scanner SDK for delivery note scanning soon after.
Now, Wolf System employees simply scan incoming goods with the progressive web app, adding them to the inventory system in real time. It also grants instant access to accurate inventory information. Thanks to the Scanbot SDK, Wolf System GmbH employees can carry out construction operations without unnecessary delay – and without having to make phone calls or physically walk to the office. The solution is already being rolled out to other Wolf System production sites.
The processes before and after the Scanbot SDKs
The process before the Scanbot SDK
Construction materials are delivered to the production site.
The delivery notes are collected throughout the day.
Workers distribute the materials in the warehouse, without adding them to the inventory system.
Three to four times a day, a worker takes the delivery notes to the office.
In the office, the delivery notes are processed manually. Now, inventory levels are updated. Delays and inaccuracies are common.
Workers have to call the office about the whereabouts of required materials.
The workers can’t carry on with their construction work, since inaccurate inventory data says the materials they need are unavailable – even when they are already in stock.
The process with the Scanbot SDK
Construction materials are delivered to the production site. Barcode labels are added to the incoming products.
The delivery note is immediately digitized through the document scanner functionality in the web app. On partial deliveries or when time is scarce, the note still goes to the office to be scanned with the app.
Workers store the materials in the warehouse. They scan their barcodes and the location’s, updating inventory levels in real time.
Workers can look up inventory levels and storage locations directly in the app, minimizing delays.
Integrating the Scanbot SDKs into the company’s progressive web app went without major hurdles, thanks to well-written documentation and responsive customer support. Wolf System GmbH could always count on quick answers and comprehensive developer support whenever questions arose. Thanks to this, their app developer team achieved results from day one.
In conclusion, integrating the Scanbot SDK provided the following benefits:
A PWA serving multiple platforms and devices from a single code base
Simple integration thanks to concise documentation
Direct developer-to-developer support via Slack